According to principles of plastic part design in post B-1~B-4 and mold concept, designers could make feasible/ producible part and mold accordingly. However, customers nowadays have more and higher requirements regarding products, they want more fashion/ personalize/ complicated designs. While part with more complicated design (aka Undercut), mold design needs more complicated mechanisms to fulfill the same.
Let’s discuss 2 concepts before we move into the main topics,
- Opening direction: Each mold has at least one opening direction, which is the direction of mold (fix and moving side) opening. The qty. of opening direction is decided by the part design. The position/ direction/ orientation of the part in the mold corresponds the mold opening direction which decides the layout of the mold.
- Undercut: A part/ mold design that mold cannot eject part smoothly.
The purpose of Mechanism is to increase the qty. of opening direction which is different from the direction of mold opening. It creates space inside mold to release undercut, therefore, the mold could eject part smoothly. with mechanism could overcome the undercut and produce parts with more complicated design.
Here discuss Core pulling: particular type of undercut.
The purpose of Core pulling is to overcome the particular type of undercut, especially the area with undercut but doesn’t allow additional parting line. see example in table-1. Core pulling is an additional / moving part similar to core pin inside mold, it attached to cylinder and guided by the tunnel inside mold. Core pulling moves inside the tunnel before mold ejects part out, see detail in table-2. Some mold design requires core pulling moves before mold open or other timing in an injection molding cycle.
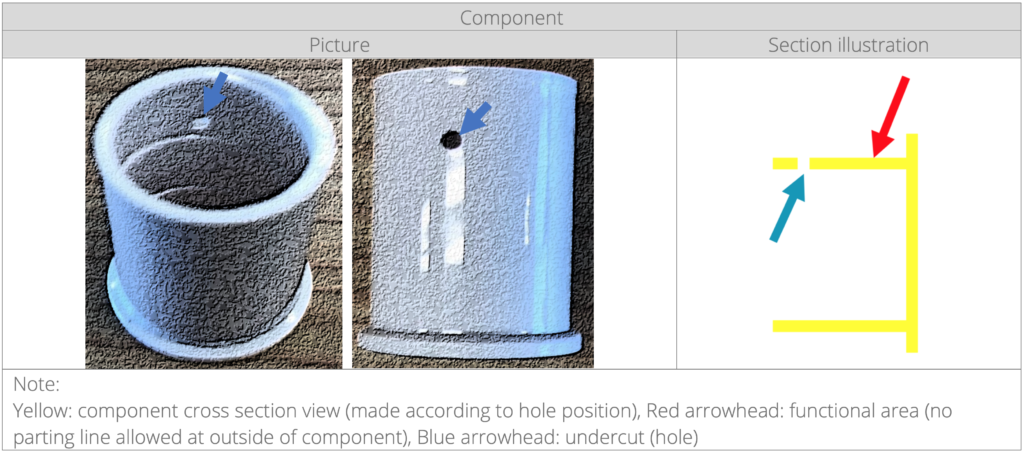
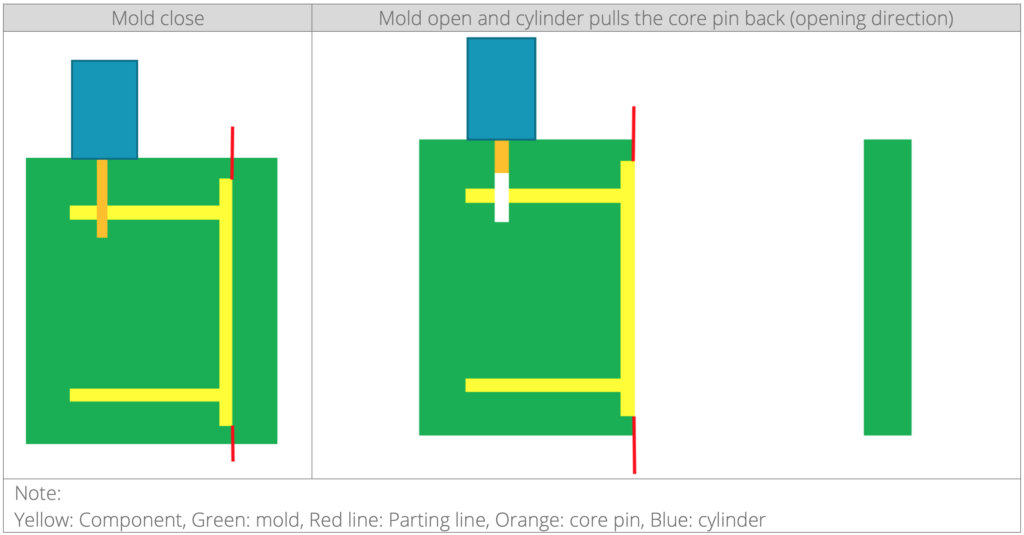