According to principles of plastic part design in post B-1~B-4 and mold concept, designers could make feasible/ producible part and mold accordingly. However, customers nowadays have more and higher requirements regarding products, they want more fashion/ personalize/ complicated designs. While part with more complicated design (aka Undercut), mold design needs more complicated mechanisms to fulfill the same.
Let’s discuss 2 concepts before we move into the main topics,
- Opening direction: Each mold has at least one opening direction, which is the direction of mold (fix and moving side) opening. The qty. of opening direction is decided by the part design. The position/ direction/ orientation of the part in the mold corresponds the mold opening direction which decides the layout of the mold.
- Undercut: A part/ mold design that mold cannot eject part smoothly.
These 2 concepts are completely tied with each other, see example in table-1 below. This is a part and 2 mold layout designs to accommodate accordingly. 1st mold layout is not a feasible mold design since it could not produce good part, the undercut could damage part while ejection. 2nd mold layout is a feasible mold design since the part could leave mold smoothly while mold open and ejection. By only changing the opening direction of mold, this mold design becomes feasible to produce same part. Opening direction and Undercut are the keys for designers to make more complicated part/ mold design.
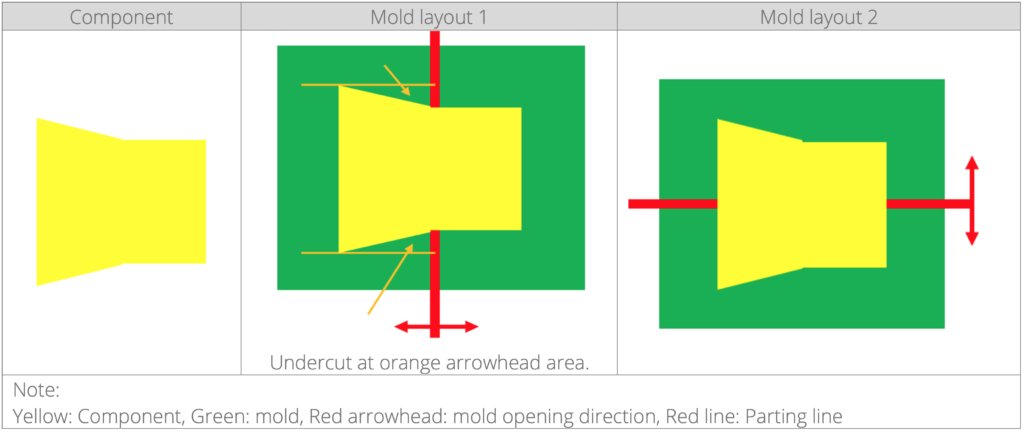
The purpose of Mechanism is to increase the qty. of opening direction which is different from the direction of mold opening. It creates space inside mold to release undercut, therefore, the mold could eject part smoothly. Mold with mechanism could overcome the undercut and produce parts with more complicated design.
Here discuss Slider: undercut locates at outer area of part.
Continue with the part and the mold layout 1 in table-1. Mold with this layout could become feasible by adding slider, it is an additional / moving part inside mold, see detail in table-2.
Slider could be driven by 2 ways: angular pin and cylinder, it depends on part/ mold design requirements, The angular pin moves slider to release undercut during mold opening, see detail in table-3. The angle and length of angular pin depending on the slider size and the distance slider shall move. If the slider is too big (heavy) or the distance is too long, it is suggested to move sliders by cylinders, see detail in table-4.
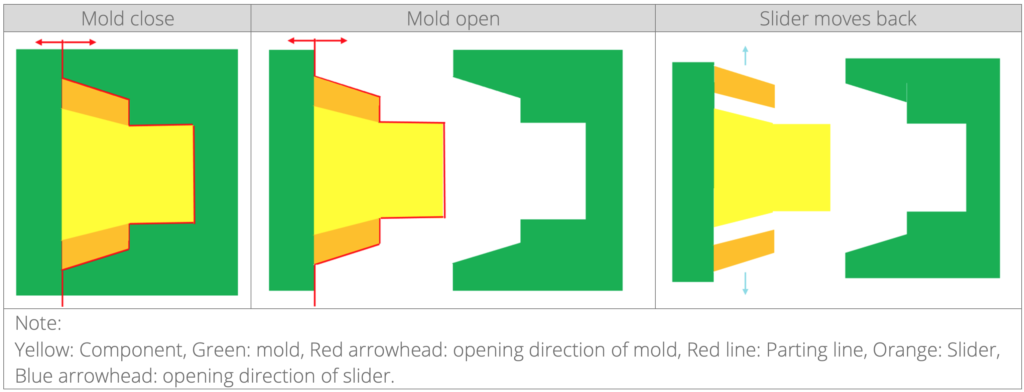
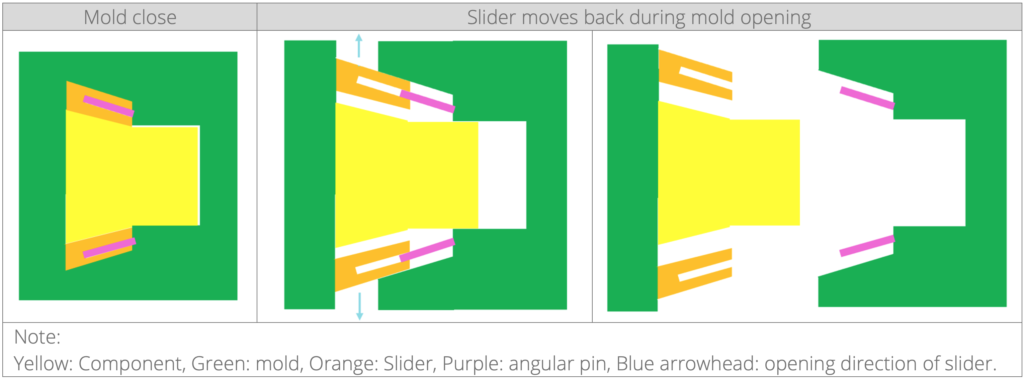
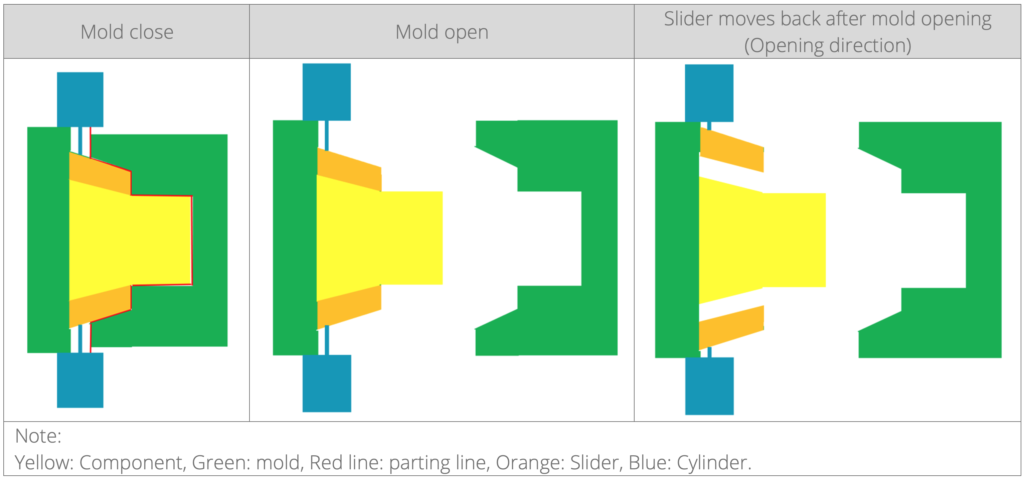