Plastic is a material which very sensitive to temperature. Previously in properties of plastic, we have discussed important plastic characteristics which are related to the same.
In a molding process, the temperature of plastic is well controlled from drying, transporting, melting (the injection molding machine heat the raw material up to process range), and of course in mold. During melt plastic injected into mold, the heat content of the material is transferred into mold. The construction of maintaining temperature in mold called cooling and the purpose of it including:
- Stabilize the process
Keep the mold at certain temperature and fully functionality. - Control part quality
The heat that was added to melt the plastic shall be removed as quickly as possible in order to produce better appearance/profile/dimension part with less cycle time.
Cooling system are consisting by many channels inside mold, see concept below:
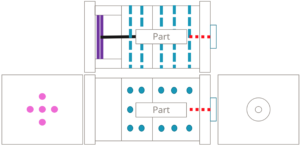
The channels inside mold are connected to temperature controller and becomes a circulation. The Material being chosen to run inside cooling channel circulation depending on the desired temperature of mold:
- Fluid
Apply Water to the mold with desired mold temperature under 100°C, apply Oil to the mold with desired mold temperature over 100°C. - Air
Applied to channel not suitable for fluid, i.e. the mold is too small to have channel diameter enough for fluid…etc.
Here discusses 2 types of cooling design used mostly in the industry,
- Direct cooling channel (Material runs through the channel directly)
Made by drilling through the mold steel block from different direction and connected with desired path. see concept below:
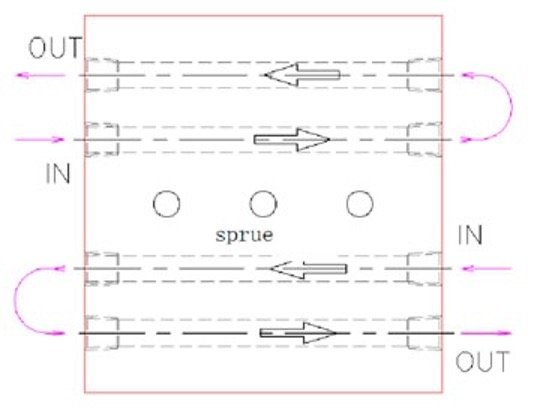
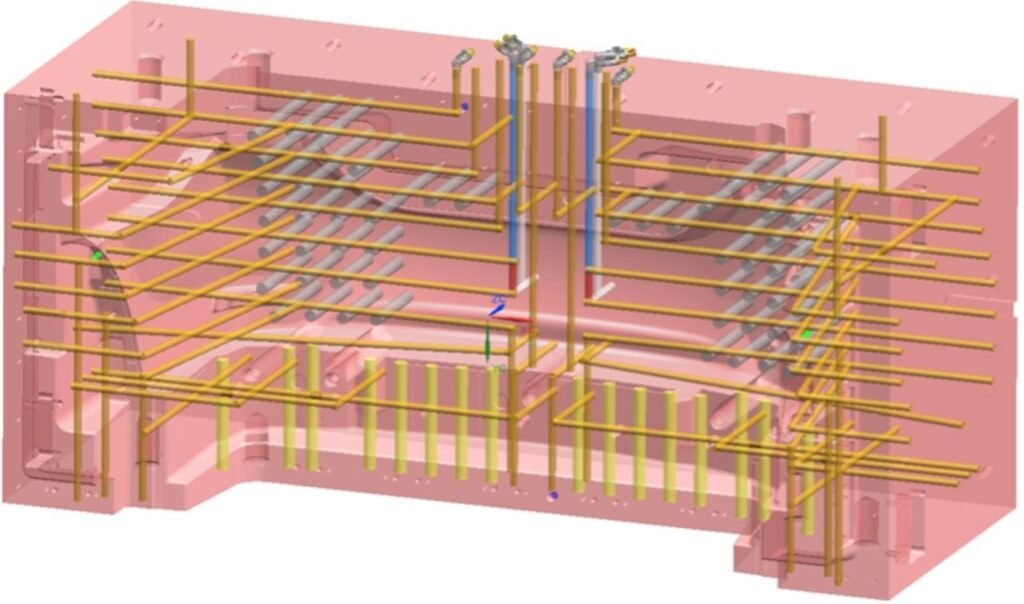
- Indirect cooling channel (Material runs through channel with certain design inside):
- Applied to area is too small to have direct cooling channel.
- Note: Green: Part, Yellow: Cooling channel, Blue: Mold steel block, Arrow: Water direction
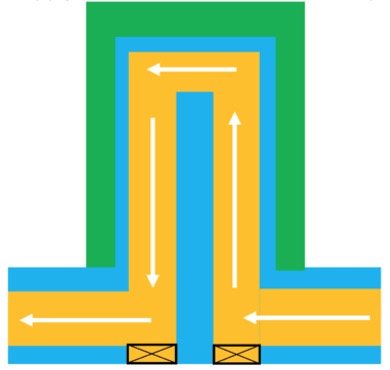
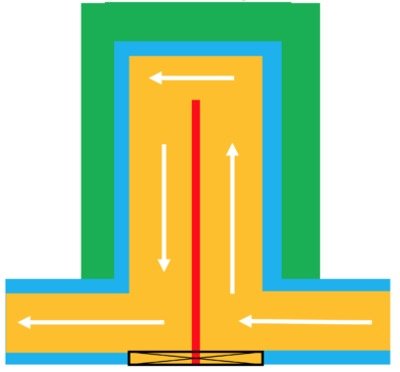
The area being covered by part decides the how the cooling channel design, cooling channel needs certain diameter to create turbulent flow and take extra heat away efficiently.
- Direct cooling channel
It could be applied if the steel thickness/strength is still enough after drilling. (Space inside cooling channel is smaller) - Indirect cooling channel
If more cooling efficiency(more space inside cooling channel) is required, we could apply Indirect cooling channel. It is consisted of direct cooling channel and additional part which is partition plate (red). After water enters the channel from one side, it changes direction with help of partition plate (red), and still travels inside same channel, then leave the channel from the other side. The Space inside indirect cooling channel is bigger than direct cooling channel.
The cooling system is designed according to part and mold design, sometimes we run channels with different temperature or material in a single mold. There are no particular rules to establish cooling as long as the extra heat brought by polymer to mold could be taken away with enough efficiency and the desired mold temperature could be well controlled.
As the industry becoming more and more competitive. New technology is kept introducing into this area, i.e. Pulse cooling system for more rapid heat transition, Conformal cooling made by metal 3D printing let cooling channel reaching more critical area in mold to provide more comprehensive temperature control…etc.