During molding process, the part shall be able to be taken out smoothly after mold open. In doing so, the part maybe damaged since it is still stick on the moving side of mold after mold open in most mold design. Since the melt plastic starts to cool down after it is being injected into mold cavity, the volume of the plastic and part size reduces because of shrinkage. The part hugs mold tight after mold open and it can not be taken out by human or robot gripper, therefore an additional “mechanism in mold/movement, step in molding process” required to help part leaves mold which is ejection system.
Ejection system is usually consisted of eject plate and ejector, it is a part of mold and driven by injection molding machine. Ejection system usually works after mold open (Pic.-1), it moved forward by injection molding machine to push part out of mold (Pic.-2)
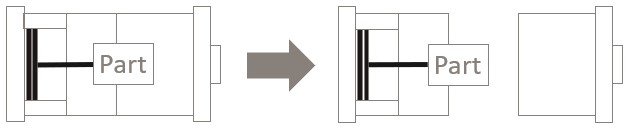
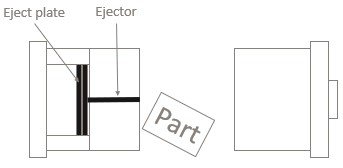
Since ejection system is a moving part of mold and it always at cavity area, the junction of ejector and cavity area is similar to the junction of moving and fixed side which has parting line. The parting line in mold appears on part as well (see example in Pic.-3) The location of ejector shall be considered carefully to ensure the surface/profile/appearance acceptable according to acceptance criteria.
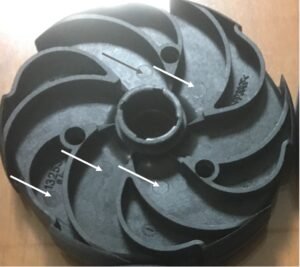
According to part design requirement, different ejector design is required to achieve the smooth ejection. Here discuss 4 elector design including:
- Eject pin
- Eject sleeve
- Eject block
- Stripper plate
- Eject pin
It provides specific area for ejection in mold. (see example in Pic.-4)
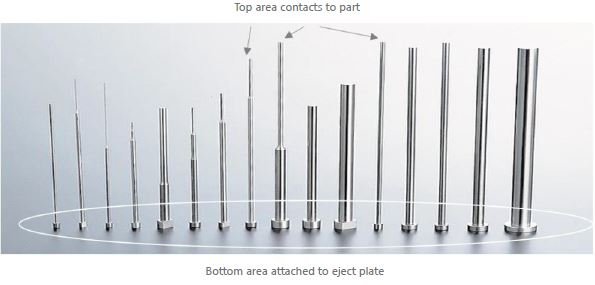
Following 2 pictures demonstrate a moving side mold that equipped ejection system with eject pin. At the status of mold open (Pic.-5) and the ejection system being driven by injection molding machine(Pic.-6). The part can be ejected/pushed out of moving side of mold by ejector pin moving forward (out of cavity of moving side of mold).
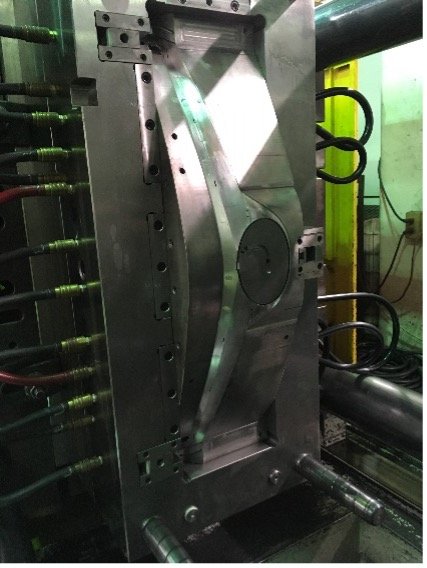
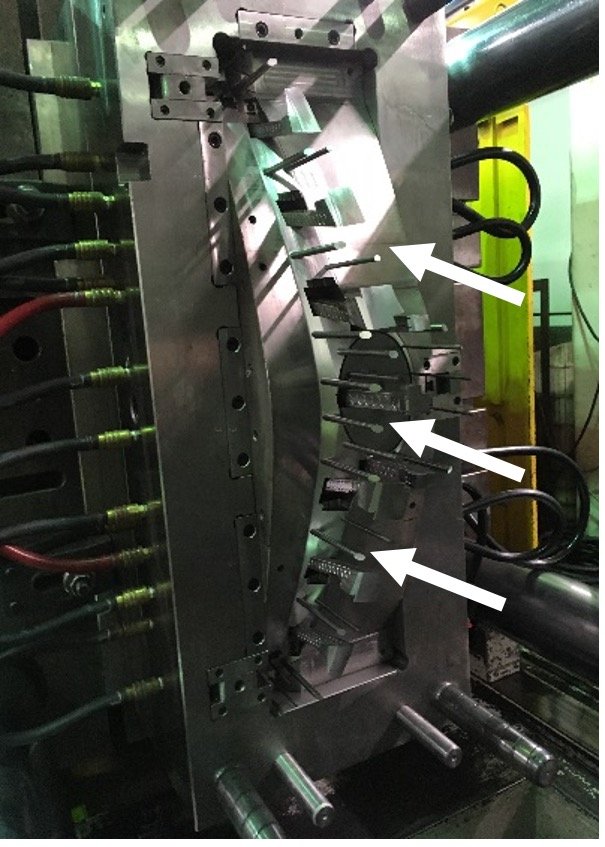
- Eject sleeve
It usually has a shape of circle at outside and hollow in the center and attached to eject plate, see eject sleeve example in Pic.-7. There would be a pin inside the eject sleeve and attach to back plate of moving side. The most part design scenario will be ejected by eject sleeve is “Boss”, see example in Pic.-8.
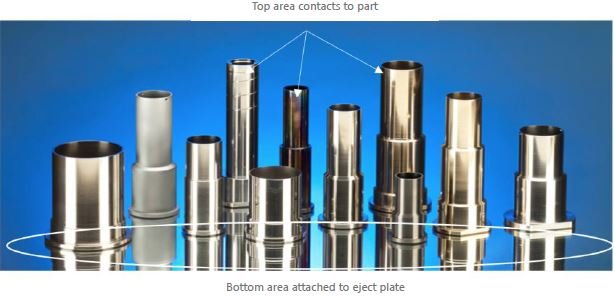
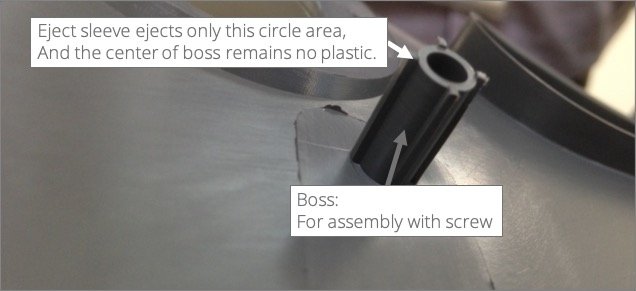
- Eject block
The contact area of part and eject pin is usually small. If the part size is big, ejection by eject pin could not provide ejection even enough to the part. Since the ejection force from eject pin concentrates too much at particular small area at part, it leads to ejector mark. White mark is not acceptable in most of the scenario, one useful countermeasure to prevent the same is to increase the contact area of part and ejection which is by using eject block instead of eject pin.
Eject block (see eject block example in Pic.-9) usually attaches to at least 2 eject rod (big eject pin) which attach to eject plate, it can prevent rotation and ensure the position of eject block in mold. Pic.-10 demonstrate a moving side of mold that equipped ejection system with eject block and the ejection system being driven by injection molding machine. The part can be ejected/pushed out of moving side of mold by eject block moving forward (out of cavity of moving side of mold).
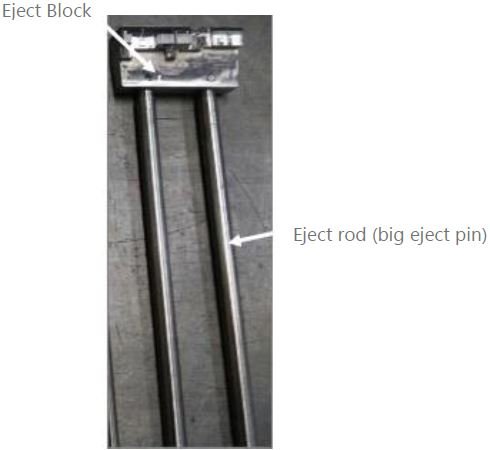
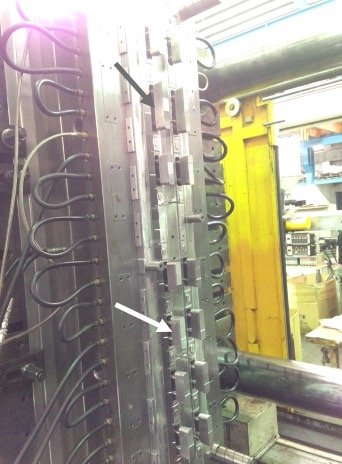
- Stripper plate
If the area of part where acceptable to have ejection mark is too small, eject part by the countermeasure mentioned above is difficult. Instead of ejector, floating stripper plate could do the job. Stripper plate is a plate attach to eject rod (big eject pin) which attach to eject plate, it could comprehensively apply the ejection to the small area acceptable for ejection of part.
Instead of moving small part of moving side as mentioned above, an entire stripper plate of moving side moves to eject part out of mold, see illustration in Pic.-11. Pic.-12 demonstrates an external part; most area of the part is appearance and eject mark is not acceptable. Only one side bottom(blue arrowhead) could accept ejection, and it is very small. Parts with similar design are mostly ejected by stripper plate.
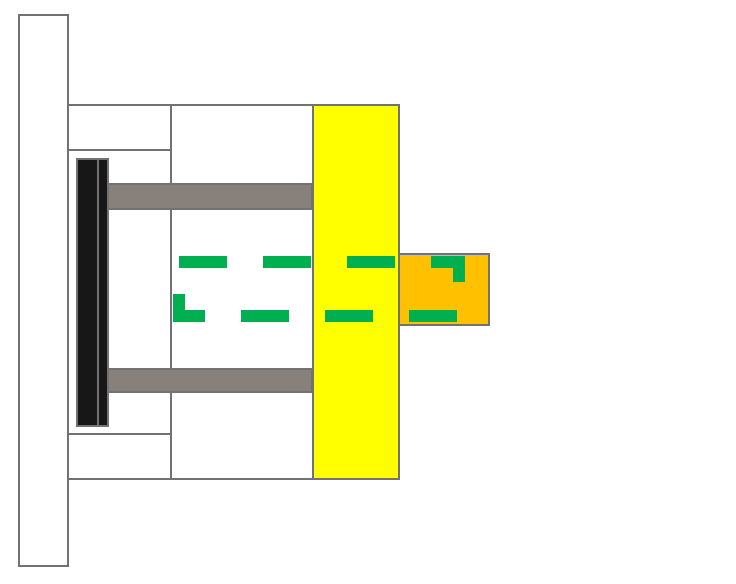
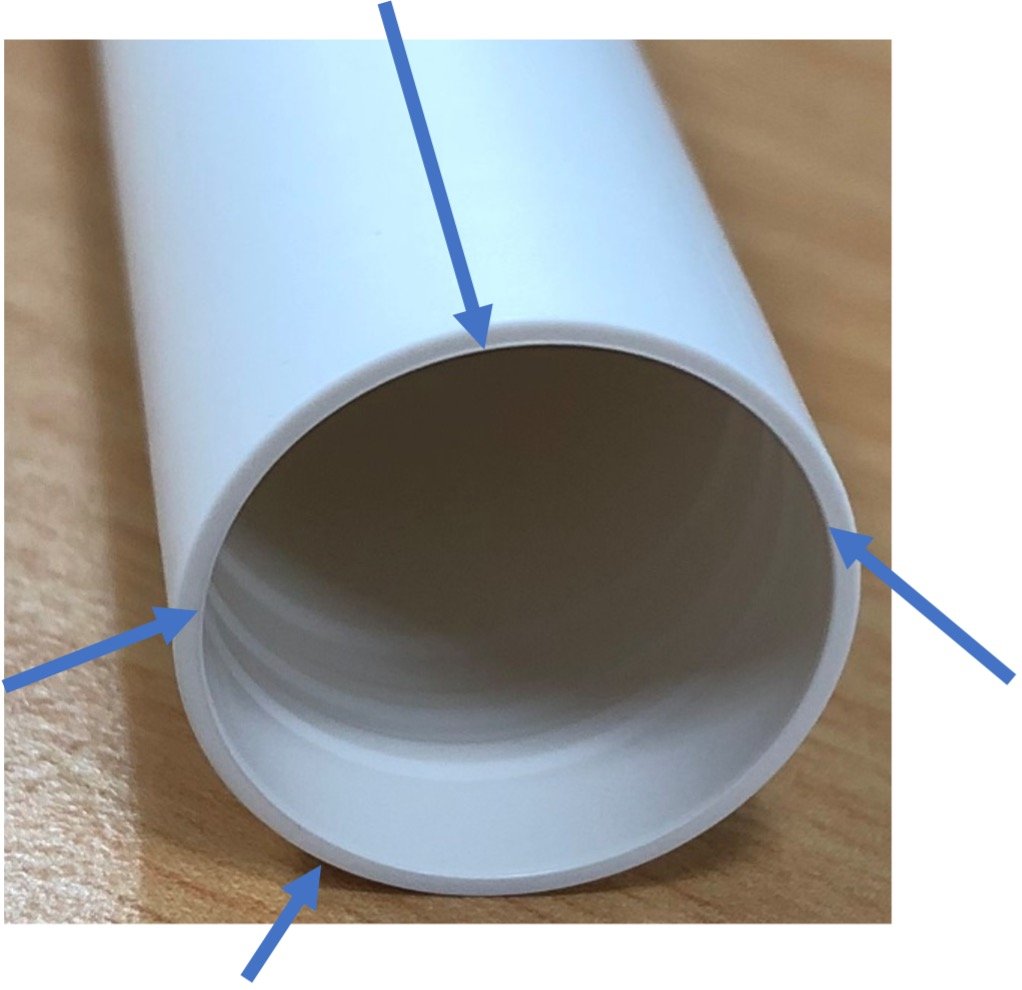
Note: 1. This is a moving side of a mold. 2. The color stands for Black: Eject plate, Gray: Eject rod, Yellow: Stripper plate (attached to eject rod), Green: Insert/cavity area for inner profile of part, Orange: part